Layout of cold rolling and ribbingplant
Place of Origin:Jiangsu China (Mainland) | Brand Name:anber |
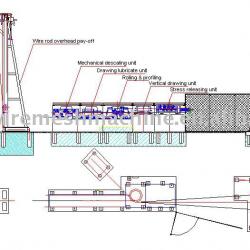
The rolling and ribbing plant is mainly used for the hot-rolled coil rod which is being wire-released, descaled, diameter-reduced by two rolling mills, relying on wire draw bench as power, then to be rolled into three-ribs, after stress relieving, then to be wound-up, bound-up by wind-up machine, becoming coiled cold-rolled ribbed reinforced bar.
No. | Name | Unit | Technical parameters | |
GZB7B (Mid. Size) | GZB10B (Large size) | |||
1 | Max. inlet dia. | mm | 8 | 11.3 |
2 | Rolling time | time | 2~4 | 2~4 |
3 | Max. rolling line speed | m/s | 1.5 | ~1.5 |
4 | Spooler coil size (mm) | d×D×b | φ460×φ800×400 | φ560×φ900×500 |
5 | Coil weight | kg | ~700 | ~1000 |
6 | Total power | kw | ~65 | ~75 |
7 | Occupy space (wire decoiler not included) | m2 | 14×6=84 | 14.5×6.5=96.25 |
8 | Workshop occupy space | m2 | 20×6=120 | 28×6.5=185 |
1. Wire decoiler
It is squirrel-cage type wire dcoiler to decoil the wire.
Loading weight: 2,500kg, height 3,500mm, diameter 600mm.
The overhead pay-off is equipped with a feeding funnel and with an emergency stop system to stop the pay-off in case of loops forming on the upper deflection roll.
2. Descaler:
To bend hot-rolled coil rod repeatedly making roll scale self-dropped. The wire goes through between driving wheel and two driven wheels, via powder box and first set of rolling mill, and wound on drum of wire drawing machine by the traction chain. Turn screw nut to press down the driving wheel to force coil rod being bent. To get satisfy descaling efficiency, you just need to control the press degree according to diameter of coil rod.
The rolls are provided with tungsten carbide rings.
Run-out scale catching box.
Safe shield.
Dusts exhaust system.
3. Lubricate powder box:
It is used to store lubricating powder and lubricate the wire feed in.
Enclosed cover to utilized the lubricant powder and prevent wastage.
Recycle storage space to reduce the wastage of lubricant and collect the unused powder.
4. Rolling mill:
There is one set each of three roller assembling equipped with various formed rolling sheets installed on both left and right worm gear cases for every rolling mill, the roller assembling are also installed on roller frame, to turn hand wheel which installed on worm axle, may resulting diameter reducing and riffling effect.
Designed as double-three roll cassettes with 2*3 forks each to carry the rolls.
Three forks each can be approached synchronously.
Including 6 cooling bolts, complete with cooling water hoses and connections.
Roll cassettes dimension: Φ147×95×15/20mm.
Tungsten carbide smooth rolls and 9 tungsten carbide ribbed rolls included.
Automatic lubrication system feed grease to all cassette rolls at a pre-setable time.
Newest technology for easy adjustment and long use.
5. The wire drawing machine:
It is special heavy-duty wire draw bench with three layers drum. The outside of drum covered with 65 Mn steel made ring so as to increase service life, the motor drives wire draw bench is the power source of the production line to achieve wire releasing and winding-up via winding
To release the stress of the wire after drawing and increase the hardness.
Vertical 14 pieces of rollers, wire diameter easy changed.
Tungsten carbide rolls.
6. The stress relieving machine:
The machine adopts two sets of damping rollers which are on horizontal and vertical direction respectively, bend the rolled bars repeatedly to relieve stress inside of bars, so as to achieve and enhance the comprehensive mechanical properties of the products.
7. I-wheel wire wind-up machine:
The machine can make the finished bar products of the production line being wound into bundle-shape automatically so as to be transported. The machine is equipped with two wire wind disks so as to that one for wire winding, the other one for binding, disk-discharging. The I-wheel adopt YLJ-type torque motor, when the diameter of wire winding disk increased, the output torque of the motor increased too, meanwhile, the winding speed and tension remains unchanged, the running speed of output axle of the motor decreased along with it.
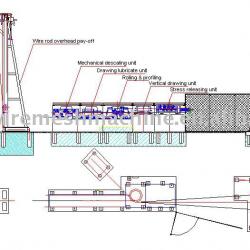
Packaging Detail:in bulk or in wooden case |
Delivery Detail:3 months or according to our order |