Dry Process Cement Kiln/Rotary Cement Kiln/Burning Furance
Place of Origin:Henan China (Mainland) | Brand Name:Dajia | Condition:New | After-sales Service Provided:Engineers available to service machinery overseas |
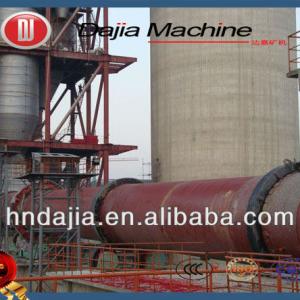
Dry Process Cement Rotary Kiln
In a modern works, the blended raw material enters the kiln via the pre-heater tower. Here, hot gases from the kiln, and probably the cooled clinker at the far end of the kiln, are used to heat the raw meal. As a result, the raw meal is already hot before it enters the kiln.
The dry process is much more thermally efficient than the wet process.
Firstly, and most obviously, this is because the meal is a dry powder and there is little or no water that has to be evaporated.
Secondly, and less obviously, the process of transferring heat is much more efficient in a dry process kiln.
An integral part of the process is a heat exchanger called a 'suspension preheater'. This is a tower with a series of cyclones in which fast-moving hot gases keep the meal powder suspended in air. All the time, the meal gets hotter and the gas gets cooler until the meal is at almost the same temperature as the gas.
The basic dry process system consists of the kiln and a suspension preheater. The raw materials, limestone and shale for example, are ground finely and blended to produce the raw meal. Contact with me via skype:gary102884 if need our cement plant. The raw meal is fed in at the top of the preheater tower and passes through the series of cyclones in the tower. Hot gas from the kiln and, often, hot air from the clinker cooler are blown through the cyclones. Heat is transferred efficiently from the hot gases to the raw meal.
The heating process is efficient because the meal particles have a very high surface area in relation to their size and because of the large difference in temperature between the hot gas and the cooler meal. Typically, 30%-40% of the meal is decarbonated before entering the kiln.
A development of this process is the 'precalciner' kiln. Most new cement plant is of this type. The principle is similar to that of the dry process preheater system but with the major addition of another burner, or precalciner. With the additional heat, about 85%-95% of the meal is decarbonated before it enters the kiln.
Basic principle of precalciner kiln.
Since meal enters the kiln at about 900 C, (compared with about 20 C in the wet process), the kiln can be shorter and of smaller diameter for the same output. Contact with me via skype:gary102884 if need our cement plant. This reduces the capital costs of a new cement plant. A dry process kiln might be only 70m long and 6m wide but produce a similar quantity of clinker (usually measured in tonnes per day) as a wet process kiln of the same diameter but 200m in length. For the same output, a dry process kiln without a precalciner would be shorter than a wet process kiln but longer than a dry process kiln with a precalciner.
Kiln and preheater tower: raw meal passes down the tower while hot gases rise up, heating the raw meal. At 'A,' the raw meal largely decarbonates; at 'B,' the temperature is 1000 C - 1200 C and intermediate compounds are forming and at 'C,' the burning zone, clinker nodules and the final clinker minerals form. A preheater tower is likely to have 4-6 stages, not the three shown here. Contact with me via skype:gary102884 if need our cement plant. Many designs are more complex but this diagram illustrates the principle. See the 'Clinker' pages for more information on reactions in the kiln.
The kiln is made of a steel casing lined with refractory bricks. There are many different types of refractory brick and they have to withstand not only the high temperatures in the kiln but reactions with the meal and gases in the kiln, abrasion and mechanical stresses induced by deformation of the kiln shell as it rotates.
Our Dajia mining company is mainly produce:
Cement plant: capacity 100TPD----6000TPD
Rotary Kiln: diameter from 1.6m to 4.8m; length from 28m to 80m
Crushing machinery: crusher, impact crusher, cone crusher, vertical crusher, ball mill, rod mill
.......
Contact with Gary for much more detials if need our machine.
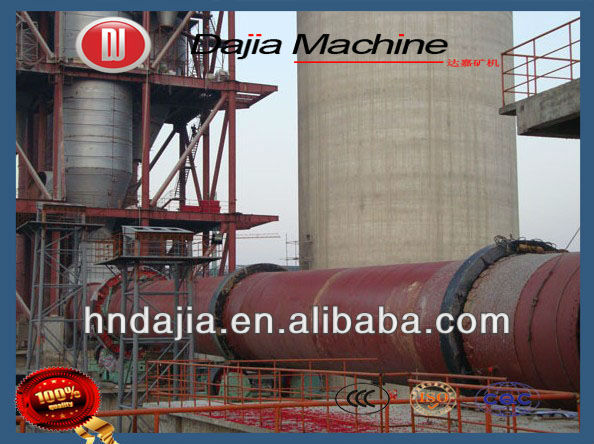
Packaging Detail:Negociated, Cause the cement plant included many machinery with various size. |
Delivery Detail:50 days |