vacuum machinery for ointment
Type:Vacuum Packing Machine | Condition:New | Application:Chemical | Packaging Type:Cartons |
Packaging Material:stainless steel | Automatic Grade:Automatic | Driven Type:Electric | Power:5.5kw |
Place of Origin:Guangdong China (Mainland) | Brand Name:Xinji | Model Number:XJJ | mixer power:5.5kw |
speed:60rpm | homogenizer power:11kw | homogenizer speed:2890rpm | material:304/316 |
main pot volume:1000L | water pot volume:700L | oil pot volume:600L | heating way:electrical, oil, steam |
apply:cream, liquid, shampoo |
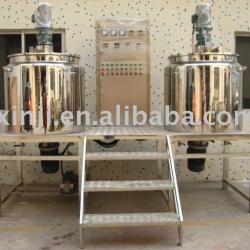
vacuum emulsifying machine Product features:
1-Feed pot which can automatic up or down; the material which in the water pot and oil pot can be directly come into the emulsification by pipeline in a vacuum state.
2-Discharging way are the emulsification pot rotary and the bottom of the pot switch valve discharging, and so on. Use the heating pipe to heating heat-conducting medium which inside the pot of the interlayer to achieve the heating of the material. heating temperature can arbitrary adjust and automatic control.
3-Put the cooling liquid into the inter layer, then it can cooling the material, Simple to operate, convenient the inter layer has keep warm function. Homogeneous systems and mixing systems can be used separately can also be used at the same time.
4-Particles of material, emulsifying, mixing, homogeneous, Dispersion are can be completed within short time.
5-Contact with the material part made by the high-quality stainless steel (SUS 304, 316 stainless steel), mirror-polished of the inner surface, the vacuum mixing device are cleanliness, it reach the health standard, in line with GMP standard manufacture. It is best for the production of the paste and cream.
operating principle:
Material which come into the emulsification pot by the vacuum pump after it heating and mixed reaction in the oil pot and the water pot. the mixing paddle and PTFE Scraper which inside the homogeneous pot are mixing the pot shape, sweep clean the sticky material which on hanging wall . so the scraped material can continuously produce new interface, After shear, compression and folding by mixing blades, so can flow to the homogenizer by mixed down way. The material which between the rotor and the stator by high-speed rotation of the homogenizer will be produce a series of processes of strong cut, impact and turbulence. particles was quickly broken into 200μm ~ 2μm, due to emulsifying pot in vacuum state, the bubble which was take away on time when the material in the mixing process.
Vessels for materials are self elevating, materials in both liquid tank and oil tank can be charged into the emulsification tank under vacuum condition through pipes, and discharged either by turning over the emulsification tank or through the valve on the bottom of the tank body.Heating process is carried out by electrothermal tubes and heat conducting medium in the jacketed shell, an injection of liquid coolant into the jacketed shell can lower the temperature inside the tank body, with the thermal insulation layer outside the jacket, temperature can be set at will and monitored automatically in an easy and convenient manner. Homogenizing system and stirring system can perform together and separately, and the processes of micronizing, emulsification, mixing, homogenizing, and separating can be conducted in short period of time. The part directly in contact with the materials is made of stainless steel with high quality (mostly commonly 304, medical 316), the internal surface is mirror polished, and the vacuum stirring system meets the GMP hygienic standard, neat and clean. Our reaction vessels are ideal devices for cream and emulsion production. Materials are heated and stirred in the oil tank and liquid tank, and then pressed into the emulsification tank by a vacuum pump once the mixing and reaction process is finished. The mixed material is then made passing through the paddles in the homogenizing tank, where the PTFE (Polytetrafluoethylene) scraping plate moves alone the vessel constantly and fittingly, cleaning all the sticky material on the inner surface, and creates a steady influx of new material. This mixture is then cut, compressed, folded over and over by the stirring paddles, and finally will move towards the lower part of the homogenizing tank, where a pair of high-speed homogenizing rotor and stator will produce power force to cut, strike, and agitate the material into fine particles. The air bubble generated in the stirring process is extracted spontaneously under the vacuum condition inside the emulsification tank. High-speed disperser: mixes and separates thick liquid or solid material with great power. Main stirring paddle: adopts infinite variable speed mechanism, which prevents the forming of more air bubbles when the material is of low temperature and high viscosity. Discharging gear rotary pump: accelerates the forming and discharging of product.
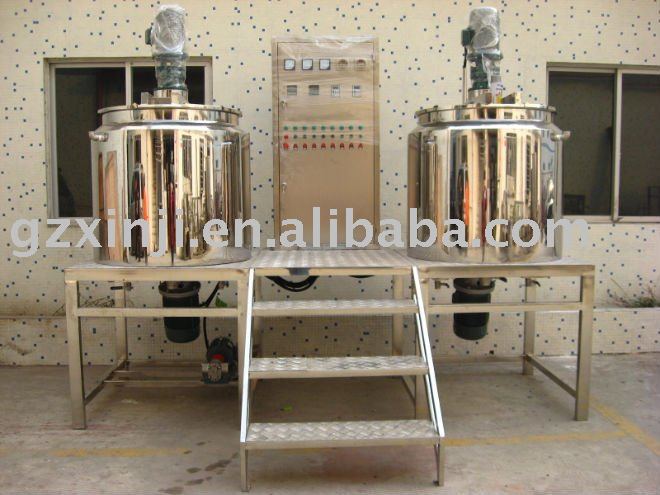
Packaging Detail:wooden case |
Delivery Detail:within 30 days |