Rinsing, Filling and Capping for PET bottles
Condition:New | Application:Beverage | Driven Type:Electric | Automatic Grade:Automatic |
Packaging Type:Bottles | Packaging Material:Plastic | Place of Origin:Italy | Brand Name:FRAMAX |
Model Number:RFCI-16/20/4-S/PK NECK | Machine finish:Stainless Steel | Type:Filling Machine,Capping Machine |
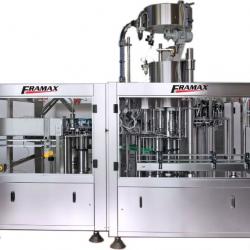
Counter-Pressure Bottling Modulblock
Hourly output guaranteed: 6.000 bph
Bottle type: 500ml cylindrical PET bottle
Product: carbonated water
Filling temperature: 0 - 4°C
MACHINE EQUIPPED OF:
Rinsing unit - fixed nozzle version – simple treatment with 16 grippers
the rinsing turret is manufactured in stainless steel AISI304. The parts in contact with the cleaning fluid are AISI 316 while the plastic parts are manufactured in alimentary industry-graded materials. Besides the machine is equipped with a lifting system to adjust the distance between the pincers and the passage level to the various bottle heights. The movement of the mechanical parts is made by means of a chain of gears that are of steel and plastic material alternatively to improve noise.
OPERATION OF THE RINSER
The bottles coming form the conveyor belt are separated by the screw and placed in correspondence with the related gripping pincers by means of the starwheels. These pincers grip the bottles tight in the zone of the neck. During the rotation of the carrousel the pincers are rotated by means of a tubular guide (twist). In this way the bottles are overturned towards the bottom and in correspondence of the washing nozzle.
16 GRIPPERS - RINSER PERFORMANCES - SIMPLE TREATMENT WITH WATER
Output: 6.000bph
Treatment total time: 5,4s
Injection time: 1,2s
Dropping time: 4,3s
Hourly water consumption: 450lt/h
Water residual for bottle (*) less than 4 gr. / lt.
(*) = The residual data is not binding. For further information's please contact us.
Counter-Pressure Filling machine with 20 filling-valves –
NECK HANDLING TYPE, without pneumatic cylinders for up-down bottles, but with stars, screw and conveyor
The base of the machine is a firmly welded structure with height adjustable supports, resistant to bending or vibration.
Upon the basement is fitted:
§ the main filler support,
§ the driving system (drive motor and a worm gear reducer),
§ the helicoidal gears which control both the entry/exit stars, and the scroll.
All components can be easily inspected thereby simplifying all cleaning and maintenance operations.
The rotary plate, supporting the filling-tank, is connected to the machine base by a bearing disc with a large diameter and guided by self-lubricating guide bushings.
The filling nozzles bolted to the isobaric tank can be easily dismantled thereby simplifying cleaning and maintenance operations.
On the electrical panel there are low tension push-button control machine and thermal relays.
In addition, safety switches are placed both on scroll and inlet/outlet stars.
ALL PARTS IN CONTACT WITH FILLING LIQUIDS ARE MADE FROM 304 AISI STAINLESS STEEL (ON REQUEST: 316 AISI)
OPERATION OF THE MODEL FILLER:
The bottles travelling on the conveyor belt are separated by the inlet scroll of the filler and passed on to the inlet star, which places them on the stainless steel bottle lifting pads by a regular and smooth rotary action.
The pressure tank, made from thick, strong stainless steel, can work at a pressure of 6 bar (tested at a pressure of 7 bar in compliance with P.E.D. safety directives). It is complete with a detachable cover, highly polished on both sides.
Float devices for product control level are located on the pressure tank cover.
On the front side of the tank there is a small inspection window.
The product source vessel is connected to the central distribution system of the filler by a feeding pipe which is fitted with an isolating valve.
Smaller pipes connect the central distribution system to the pressure tank.
The filling nozzles are fixed to the pressure tank by means of bolts which can be easily dismantled.
The bottle aligning guides are made in stainless steel AISI 304.
The stainless steel filling nozzles are made specifically for FRAMAX by highly specialized workshops.
Perfect sterilization and faultless reliability of the system are guaranteed.
Listed below, are all nozzles suitable for high pressure filling cycles:
"S" FILLING NOZZLE
Suitable for high pressure filling of products like mineral water, fizzy drinks and sparkling wines
Once the bottle has been placed directly under the filling nozzle, the pressure valve is opened so as transfer some of the pressure which is contained in the tank of the liquid to the empty bottle. When the pressure in the bottle is the same as the pressure in the tank, the nozzle is opened by a spring so that the filling cycle starts.
The liquid which goes into the bottle is spread along its sides by a rubber packing mounted on the levelling tube. As soon as the liquid reaches the hole on the levelling tube the filling nozzle is shut. The filling nozzle is mechanically shut off by a control cam and another cam opens the valve for reducing the pressure inside the bottle. Finally the bottle, now filled with liquid both still and levelled, is [being] transferred to the outlet star.
The accurate construction of the valves guarantees perfect functioning and closure even at very high pressures. In case of partial or total bottle breakage's, the valve, due to its sensitivity to differences in pressure, shuts off immediately so as to avoid the spread of compressed gas or liquids.
AUTOMATIC 4-HEADS ROTARY CAPPING TURRET
suitable to apply one format of FLAT plastic pre-threaded screw caps Ø 28 mm on one format of PET round bottles, for a production rate up to 6.000 BPH/Requested.
Turret equipped with:
· Automatic centrifugal sorter, made of AISI 304 stainless steel, equipped with cap level monitoring device.
· Chute, made of AISI 304 stainless steel, equipped with electronic cap-presence monitoring device.
· Pick & Place device, made of AISI 304 stainless steel.
· PK310 capping with optical reading of the static torque settings; made of AISI 304 stainless steel.
· Bottle neck supports to firmly hold the containers during screw-capping and to prevent them from being crushed; a solid outer guide in stainless steel, anchored to the capping machine's support structure by means of stainless steel columns, keeps the bottles correctly positioned inside the neck supports.
· Turret suitable to be inserted onto the Modulblock’s central shaft.
TECHNICAL FEATURES CAPPER:
- Speed: 6.000bph
- Product: carbonated water
- Packing: 500ml and 1500ml PET bottles (MAX diam. 110mm)
- Closure: FLAT plastic pre-threaded screw caps diam. 28mm over longer than height. Only on PET bottles
GENERAL TECHNICAL FEATURES MODULBLOCK:
Turrets raising: rinsing, filling, capping machines: ELECTRICAL
- Manual lubricator with greaser
- Set of adjustable feet with M30 stainless steel bar
- Standard direction: from left to right (clockwise) ( anticlockwise on request and with surcharge )
- Machine to be placed in line without conveyor pulling, collection table, belt-transmission, conveying-chain
- Machine equipped for one diameter of cylindrical bottle, one cap format
- Bottles conveyor-belt in AISI 304 stainless steel (standard closed type section 100*100mm)
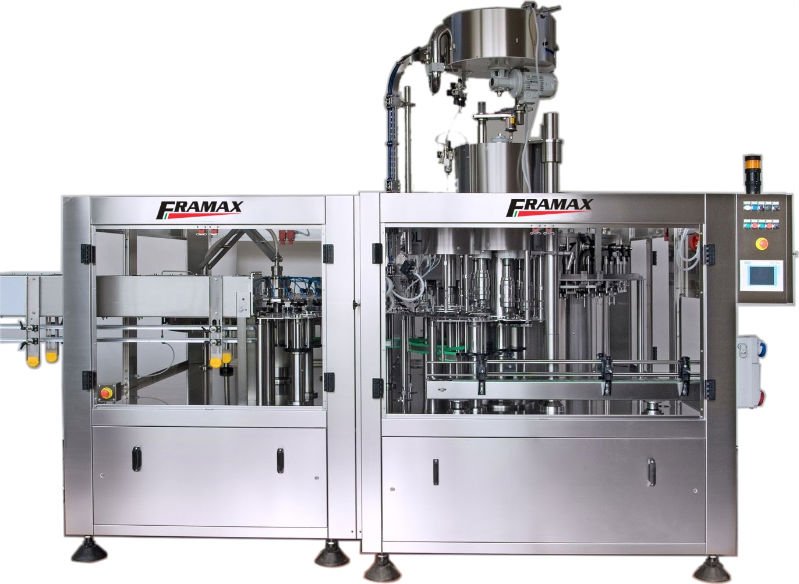
Packaging Detail:Machines on seaworthy pallets |
Delivery Detail:2-3 months according to workload |