MDF Production Line / Medium Density Fireboard Production Line /Fiberboard Making Machine
Condition:New | Type:Woodworking Planer | Place of Origin:Chongqing China (Mainland) | Brand Name:CMMC |
Model Number:SC-300 | Voltage:380V | Power(W):550KW | Dimension(L*W*H):100*100*30 |
Weight:300-500MT | Certification:Yes.ISO9001 | Warranty:3 Years | After-sales Service Provided:Overseas service center available |
Output Capacity:10,000 M2~300,000 M2 | Process:Multi-Opening Hot Press |
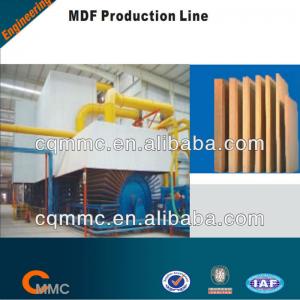
MDF Production Line / Medium Density Fireboard Production Line /Fiberboard Making Machine
1. CMMC can provide complete technology and high-quality equipment for MDF Production Line .
2. CMMC had designed and construction over 30 Sets of MDF Production Line in China and Overseas Such as Korea,Jordan, Vietnan,Indonesia
3. CMMC has very professional enginieering experiece and has high expericed Pocess / Mechanical / Electrical / Instruction engineers and technicians.
4. CMMC will provide fullly support for the customers during Construction, Commissioning and Production for MDF Production Line Project.
Production process of MDF line
MDF production line consists of following sections:
1.wood preparing section:
Wood preparing section
In order to improve fiber separating quality, prolong wood soften time, decline separating time & power supply consumption and increase productivity, reduce production cost, a special designed pre-heater with 2 grade horizontal preheat before defibrator. It makes this section has longer pre-heating time, the pre-heater needn’t control material level than traditional MDF vertical preheat. Because 2 grade preheat, wood plasticity is greatly improved. Uniform, complete, good ventilation and elasticity, tensile strength fiber that closes to natural wood can be got. Quality of MDF board greatly increased.
The raw material mainly is wood chip from small diameter wood log, saw dust of 5-10% of total weight can be added in wood chip, the small pieces of ply wood can be used but the piece size should be less than 50x50mm and the quantity less than 20% of total weight.
2.Fiber gluing section:
Adopt traditional jet pipe to spray glue. Match a glue nozzle in a jet pipe which defibrator to pipe drier. Glue metering pump transfers stable solid content glue into nozzle and at the same time input compressed air to make glue foggy, mixing uniformly with fiber which is in high speed turbulent state and rolling state.
3.Fiber drying section:
Fiber drying adopts 1 grade air dry. Because wet fiber enters drying pipe, its speed lows greatly drying media speed, under high temperature gradient state, moisture of wet fiber quickly vapor, and moisture content reduces rapidly. Through control drying media temperature & flow, moisture content of fiber reaches process requirement. There is a spark detector & extinguishing system in the drying pipe to reduce fire probability least.
4.Fiber storage and metering section:
In order to avoid material supply and bridge problems in vertical bin, fiber metering bin adopts horizontal bin type. To guarantee uniform fiber supply, The bin should keep some fiber level, so a fiber level instrument is installed in the bin and carries electric interlock control together with drier & forming machine. There is a ventilation hole in the chip bin and tail door can be opened by air-driven. When fire or accidents appear, scraper in bottom of bin can be reversed and fire chip can be discharged. Out-feed is controlled by rotational speed of out-scraper and it will be displayed through electric belt weigher.
5.Forming section:
Adopt vacuum air forming machine or mechanical forming machine in this section. After drying, fiber mixes with air, it uniformly spreads on the moving net in high speed air flow type. There is a negative pressure tank under net, avoiding fiber splash. Drying fiber is adsorbed in the net and forms gradually uniform mat. Flight roller outside forming chamber absorbs redundancy fiber away and conveys to metering bin. The lower of forming tank is vacuum tank. It uses centrifugal ventilator to form negative pressure. The medium of Vacuum tank is lower vacuum zone, two sides are high vacuum zone and can be adjusted vacuum through air door. So two sides density of mat is higher than medium mat. A continuous belt pre-presser is equipped in prepress section. Mat moves under pressed state. Pre-presser has two parts, one is helix angle guide part, its distance can be adjusted according to mat thickness. The other is pressurizing & keeping pressure part. Mat is pressed to initial strength mat under some linear pressure. After pre-pressing, conveying is divided into three section. The first is speed-up section. Pre-pressed & cut mat is separated rapidly. The second is test section. Waste mat is conveyed to mat return device, then sends to metering bin. The third section is to convey qualified mat to hot press.
6.Hot pressing section:
Hot press is a single- opening press based on capacity of the line . Steel belt sends pre-pressed mat into hot press. Single lifting oil cylinder lifts quickly. It greatly increases lifting speed than traditional hot press and improves board surface pre-solidify, decreasing board surface sanding thickness. After hot pressing, blank mat is sent into combined cutting section by conveyer and cut to the same dimension board.
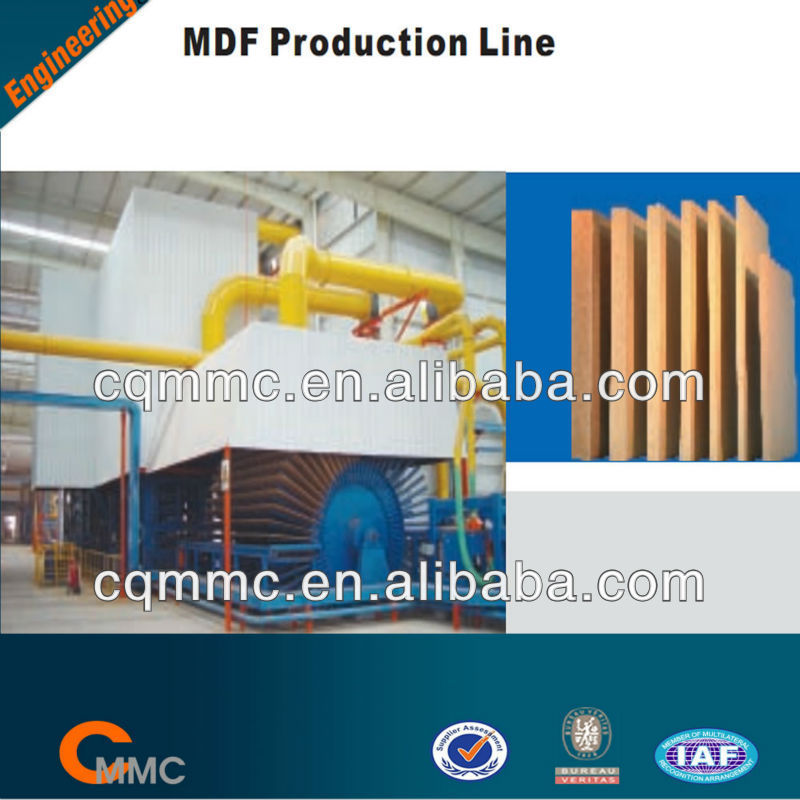
Packaging Detail:Wood Box or Steel Frame Box |
Delivery Detail:3-6 Month |