industrial mechanical robot arm for multifunction
Condition:New | Elevation Speed:180°/s 1 m/s | Vertical Travel(mm):850mm | Horizonal Travel(mm):850mm |
Application:Welding | Place of Origin:Denmark | Brand Name:UR | Model Number:UR5 |
Weight:45.1 | Dimension(L*W*H):475 mm x 423 mm x 268 mm | Power(W):200w |
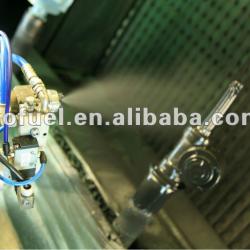
Mechanical robot arm
1.Robot handles microscopically small parts
Modern hearing aids are becoming smaller and smaller so that you can barely notice them nestling in someone’s ear. This makes great demands on precision in production. The hightech hearing aid manufacturer Oticon now uses robots from Universal Robots to handle parts that are just a millimetre long.
Oticon has been using robot technology for the last ten years, but the innovative trend towards almost invisible hearing aids means that very small parts have to be manufactured and assembled.
The robot is securely fitted to the injection moulding machine and can move over the mould and pull up the plastic items. This is done using a specially designed vacuum system which ensures that the sensitive items are not damaged.
Oticon also uses the robot for a different task in the foundry where the suction tool is replaced with a pneumatic gripping tool used for handling more complex cast parts. The robot works in cycles of 4-7 seconds.
“Parts for modern hearing aids are often around one millimetre in size, so we need a solution that is able to draw small parts out of a mould. It’s impossible to do this manually,” says Arne Oddershede, who supervises the maintenance unit at one of Oticon’s manufacturing plants.
The large two- and three-axis robots, which Oticon used in the past, were no longer up to the task. Movements that only go in and out and up and down are not good enough.
“If a small part is in a mould, for example, you may have to tilt it,” says Lars Gasberg, Sales Manager at Armiga, the system integration specialist that distributes Universal Robots’ products.
2. Larger range, smaller production runs
Another challenge associated with Oticon is that the company is offering more and more variants and models but in smaller production runs, which have naturally been manufactured in the most economical way possible.
“We have switched to Universal Robots because
we wanted a more flexible solution which is also financially viable for smaller production runs. It’s important that the robot is easily accessible and designed in a logical way, as well as being easy to reprogram. Specialists are required where traditional robots are concerned, but with this robot all our technicians are literally able to take the robot and show it the movement pattern,” Arne Oddershede says.
It only took one day to install the robot for its new task in Oticon’s foundry where it handles very small parts such as wax filters measuring no more than one millimetre, if that.
3. Robot expands production capacity
Every night a robot from Universal Robots works diligently and completely unmanned next to a milling centre at the Thiele tools company. In this way Thiele has now manufactured many more small series without additional personnel or having to buy more machinery.
The global financial crisis meant several challenges for Thiele and most other small and medium-sized companies. In order to increase productivity, the company was on the lookout for new business areas and is therefore now also investing in milling small series. The economic situation meant that Thiele was unable to employ additional employees or buy new machinery.
Automation turned out to be the solution: when manual single production finishes in the day shift, the robot is placed next to a milling centre and runs an unmanned production of small series at night. It relieves employees from monotonous handling work so that they can carry out far more challenging tasks instead.
4. No need for a safety shield
The robot also carries out quality assurance using an image processing system developed by the distributor Faude and integrated into the Universal Robots solution.
There was no need for Thiele to make design changes in order to implement the automation solution: Universal Robots has had its industrial robot certified so that it can work right next to humans without an additional safety shield.
The robot solution was developed and integrated in just four weeks. Since then the system has run without problems.
5. New perspective on industrial robots
Universal Robots is also solving a classic dilemma for smaller companies.
“A small craftsman’s business can’t just buy a robot with standard tools. It needs an individual solution suitable for the company’s environment and special working requirements. Until recently the price of robot systems has been too high for them, although Universal Robots’ lightweight robot at a third of the price for similar solutions gives smaller companies a whole new perspective on industrial robots,” explains Dieter Faude from the distributor Faude.
ABOUT Thiele: Thiele is a classic small tools manufacturer that develops individual solutions for designing processing, testing, measuring and leakage testing equipment and manufactures parts in CNC controlled machining centres. The company has around 10 employees and primarily manufactures individual parts and small production series for industry. Its customers are mainly companies within the automobile industry, aeronautics and space technology and plastic production.
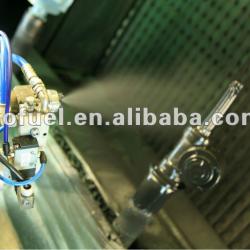
Packaging Detail:Carton Boxes |
Delivery Detail:10 days after payment |