HOT!!! raisin drying machine energy saving 75%
Place of Origin:Guangdong China (Mainland) | Brand Name:KINKAI | Model Number:JK10RD | Type:Dryer |
energy save drier:new industrial dryer | heat pump dryer:low cost heat pump dryer | power input:6.2KW-11.5KW | heating capacity:22-35KW |
cooling capacity:16-25KW | current:20A | dehumidify amount:20-40L/H | drying type:circulating drying |
cover:galvanized steel | stainless steel:option |
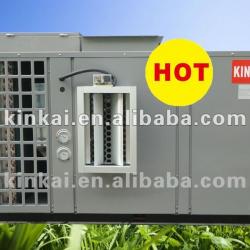
1. heat pump dryer running cost just as 40% of oil dryer, 50% of coal burning boiler, 30% of electric boiler;
2. Max temp: 80C;
3. during drying, the material does not craze,does not distortions, nondiscolouring,never degenerate, non-oxidize, drying completely,with good Rehydration, keep nutrient content;
4. energy saving and enironmental protection.
5. cooling drying,heating drying and dehumidify all in one;
6..Conventionally, materials are dried either in the field (sun drying) or using
high temperature dryers (electric, gas fired, etc.). Successful outdoor drying
depends upon good weather and indeterminate weather can render a product
worthless. High temperature drying can damage the nutrient content and impart an
unpleasant smell to the dried product.
Specialty crops such as ginseng, herbs, echinacea, etc.,
need to be dried at low temperatures (30 - 45Celsius degree) for product quality
optimization. This is an important consideration as they have a relatively high
commercial value. Heating ambient air to use for drying, although a simple
cost-effective procedure, is of limited application, particularly at higher
ambient air relative humidities because of the low allowable maximum temperature
conditions. Under high ambient moist air conditions, it may not even be possible
to dry the material by conventional means. High temperature drying deteriorates
the material structure and can render it unsuitable for further use. Low
temperature drying of specialty crops reduces the risk of loss in nutrient
content and damage to physical properties. Drying system incorporating a
dehumidification cycle have been developed that both conserve energy and handle
the material gently. The dryer operates using a heat pump where both sensible
and latent heats are recovered from the exhaust air. The heat is then recycled
back through the dryer by heating the air entering the dryer. The heat pump
drying system is a combination of two sub-systems: a heat pump and a
dryer.
The heat pump operates according to a basic air
conditioning cycle involving four main components: the evaporator, the
compressor, the condenser and the expansion valve.
The working fluid (refrigerant) at low pressure is
vaporized in the evaporator by heat drawn from the dryer exhaust air. The
compressor raises the enthalpy of the working fluid of the heat pump and
discharges it as superheated vapor at high-pressure. Heat is removed from the
working fluid and returned to the process air at the condenser. The working
fluid is then throttled to the low-pressure line (using an expansion valve) and
enters the evaporator to complete the cycle.
In the dryer system, hot and dry air at the exit of
condenser is allowed to pass through the drying chamber where it gains latent
heat from the material. The humid air at dryer exit then passes through the
evaporator where condensation of moisture occurs as the air goes below dew point
temperature.
A performance study of a heat pump dryer system is
required to fully understand its operating characteristics based on different
materials to be dried. To accomplish this objective, the project was divided
into three tasks (steps). Task A is concerned with the design and construction
of a prototype heat pump dryer system. Task B involves field-testing of a
prototype system using specialty crops or material with similar characteristics.
Finally, task C is to develop a comprehensive computer model using the
fundamentals of thermodynamics for a heat pump dryer system and to determine its
accuracy compared to experimental results.
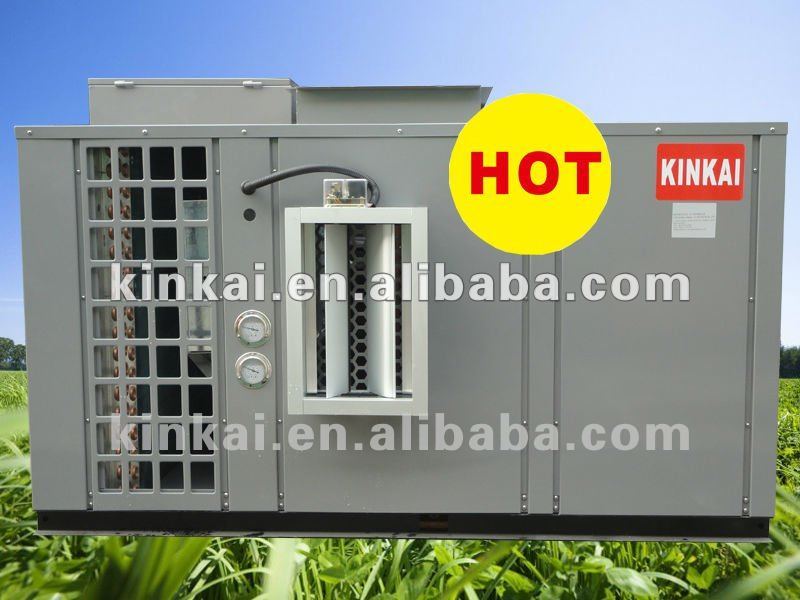
Packaging Detail:plywood |
Delivery Detail:20days after deposit |