DPL Fluid Bed Granulation, Drying, and Coating
Place of Origin:Chongqing China (Mainland) | Brand Name:Jinggong | Model Number:DPL series | Application:Granules |
Type:Granulator | After-sales Service Provided:Engineers available to service machinery overseas | Production Capacity:15kg-500kg | Packaging:Wooden Box |
Anti-explosion Optional:2 bar 10 bar 12 bar | Operation system:Simens PLC with touch screen | Material:SS316 and SS304 | Standard:GMP |
Certificate:CE | Voltage:220/380/460 based on your requirements | Warranty:2 year | Heating method:Electric heating or steam heating ,up to your choice |
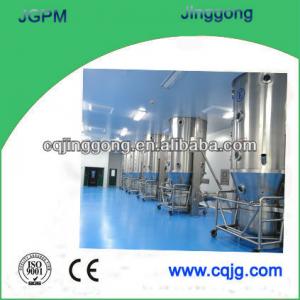
DPL Fluid Bed Granulation, Drying, and Coating:
Purpose designed for cGMP processing of fine powders, pellets, granules, crystals and tablets.
Fluid bed drying
Gentle, rapid drying of powders and particles
The product to be dried is fluidized by passing hot air through it. The process achieves fast heat transfer making it very efficient, yet gentle on the product.
Capacity: from 50g to several kg /batch or several kghr
Batch fluid bed processing has been used in the pharmaceutical industry for the past 30 years. Figure 1 shows the components of a typical fluid bed processor. The technology was originally developed specifically for rapid drying. Over the years, fluid bed processing has come into routine use for other applications such as granulation, agglomeration, air suspension coating, rotary pelletization, and powder and solution layering, but the principle of the fluid bed processor has not changed.
FL-B fluid bed granulator is a good choice for making particles, mixing powder, and drying processes in pharmaceutical, food, feed, and chemical industry. This equipment complies with the state standard GB12254-90. The particles are used as instant drink granules and for filling capsules or compressing tablets
2 bar or 10 bar
Fluid bed processing involves fine dust and dry process air, which can cause an explosion triggered by a static charge. Such an explosion creates a momentary overpressure in the processor. Until late in the 1970s, the fluid bed processorwas capable of withstanding only 2 bar overpressure. A 2-bar unit required a pressure-relief duct to vent the over-pressure in case of an explosion. The processor had to protrude through the roof or be installed near the outside wall of the facility to minimize the length of the pressure-relief duct. The processor required doors equipped with gaskets, posing a cleaning problem. It was thought that a machine capable of withstanding higher pressure was very expensive to make. However, 10-bar, pilot-size units were introduced by some manufacturers in the late 1970s.
A 10-bar unit does not require a pressure-relief duct and thus can be installed anywhere within the building. This also meant that the pressure-relief duct, doors, door gaskets, and cleaning problems due to doors and gaskets were eliminated. In the 1990s one can obtain a production unit with a 10-bar shock resistance.
Air-handling unit
For a fluid bed processor used in manufacturing, process air is generally drawn from the outside of the building. The conditioning of this air to a constant humidity and dew point is now considered essential. The drying capacity of the air depends on its temperature, humidity, and volume. Because of the globalization of the pharmaceutical industry, fluid bed processes must be able to be transferred from one location to another anywhere in the world. To ensure the consistency of the process conditions and thus the product produced, it is important that the quality of the process air be consistent and re-producible. The recent trend is to have an air-handling unit that can produce air of consistent quality with the desired dew point throughout the year.
wash-in-place design
Main technic data sheet Extract Machine for Granulating /Coating
FL-B Main parameter (as reference) | |||||||||
Specification | Model | ||||||||
Specification | Denomination | 15 | 30 | 60 | 120 | 200 | 300 | 500 | |
Material Container | Volume | L | 45 | 100 | 220 | 420 | 670 | 1000 | 1500 |
Dimension | mm | 550 | 700 | 1000 | 1200 | 1400 | 16000 | 1800 | |
Capacity | Kg/batch | 15 | 30 | 60 | 120 | 200 | 300 | 500 | |
Steam | Pressure | Mpa | 0.4--0.6 | ||||||
Steam flow | Kg/h | 20 | 60 | 120 | 140 | 180 | 310 | 400 | |
Compression air | Pressure | Mpa | 0.4-0.6 | ||||||
Steam flow | m3/min | 0.6 | 0.6 | 0.9 | 0.9 | 1.1 | 1.1 | 1.5 | |
Blower | Kw | 3 | 5.5 | 11 | 18.5 | 22 | 30 | 45 | |
Heater | Kw | 12 | 21 | 30 | 48 | 87 | 163 | 185 | |
Noise | db | less than 75 db | |||||||
Tower Dimension (mm) | A | 1900 | 2100 | 2250 | 2650 | 2800 | 3500 | 4000 | |
B | 1350 | 1800 | 2400 | 3200 | 3800 | 4200 | 4200 | ||
C | 380 | 420 | 480 | 500 | 520 | 600 | 680 | ||
D | 700 | 1100 | 1320 | 1420 | 1640 | 2000 | 2260 | ||
E | 700 | 860 | 1000 | 1200 | 1400 | 1600 | 1800 |
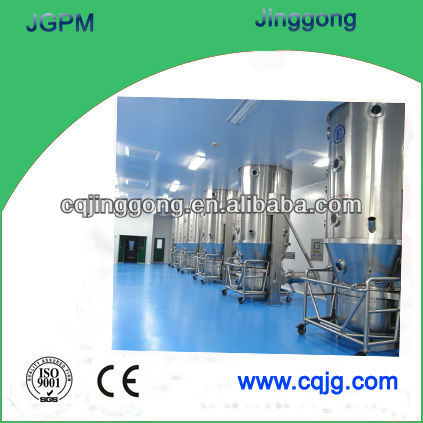
Packaging Detail:Standard wooden cases |
Delivery Detail:Within 45 after prepayment |