2013 high quality CE approved poultry feed machine
Condition:New | Place of Origin:Henan China (Mainland) | Brand Name:Hengmu | Model Number:SZLH |
Type:Feed Pellet Machine | Voltage:380V | Power(W):160kw | Dimension(L*W*H):10350*12500*10880 |
Weight:8950 kg | Certification:CE, SGS, BV | Warranty:1 year warranty | After-sales Service Provided:Engineers available to service machinery overseas |
Color:special designed according to your needs | Motor:Seimens | Bearing:SKF | Cooler:Counterflow cooler |
Output:20% higher efficiency | Mixing time:40-120seconds/batch | Evenness degree:CV≤5% | Capacity:5-20t/h |
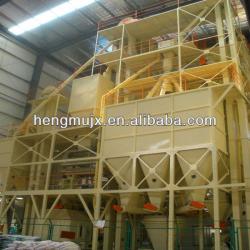
2013 high quality CE approved poultry feed machine
Company introduction:
Our company is located in northwest of Henan Province, 80km away from provincial capital zhengzhou.The material we using is 2mm thicker than feed machinerystandard, besides, we offer you 24hours rapid response for full-time.
The main process for 2013 high quality CE approved poultry feed machine:
The whole process:
Raw material- cleaning---crushing---mixing---pelleting---cooling---crumbling---sieving---packing
The first section: the cleaning section.
1. Feed machinery ---cleaning section:
Before going into the main equipments,the raw materials should be cleaned to remove impurities and iron parts in order to ensure the product quality and normal working of the main equipments.
The main task of this section is :
A. To clean the material in order to ensure the quality of the products and the regular working of all equipments.
B. To scale different meterials according to the formula and send them to the crushing section.
The raw material go through the bucket elevator, then it will be lifted into a certain height, then it goes into the pre-cleaner, in which the impurities can be removed; then the clean material goes into the permanent magnetic sleeve, in which the iron things are removed, then clean material goes into the crushing section.
The second section: the crushing section.
The task of this section is to crush the clean materials we got in the last section into powder,and then deliver the powder to the next section.
The clean material goes into 201(the bin for crusher), 202 is the pneumatic gate, then goes into 203(the auto feeder), which is to ensure the full-load working of the crusher; Then the 204 is the crusher, the crusher can crush the material to certain required size, to meet the feed formular. From 205-207, it is called the negative pressure air induction system, which is to handle with the material which stayed in the crusher. The 208 is belt conveyor, from which the crushed material will be conveyed to the next section without air flow.
The third section: the batching and mixing section.
The task of this section is:
A. evenly mix different materials into complete powder feed.
B. According to the certain operation order between the bin for the mixer, the mixer and the buffer bin,to ensure the continuous operation.
The material which is no need to be crushed goes into the conic powder sieve, in which the impurities are removed. The material, which is crushed in the last section, is lifted by the bucket elevator, will go through the rotary distributor, then the material enters the batching bin. There are high and low level indicators in the batching bin, the signal of the high level indicator shows the batching bin is full, and the low level indicator shows there is no material in the batching bin. The signal will be transmitted to the central control room, which command the feeding workers to fill the bin. Then under the PLC control, the discharger, the batching scale and the scale gate coordinate mutually(cooperate with each other), weigh the material accurately, to achieve the continuous material supply. Different materials use the same scale, after one material is weighed, the discharger will be closed, then another material will be weighed. After all materials are weighed, the computer will test the mixer, when receiving the signal of the mixer, the pnuematic gate will open, and all batching materials go into the mixer. After full mixing, the bottom door of the mixer will open, and the material enters the buffer bin, then the mixed materials will be delivered by the scraper conveyor to the next section.
The fourth section: the pelletizing section.
The task of this section is to pelletize the powder feed to required sizes.
The process of this section is: Powder feed that comes from the last section is conveyed high by the elevator,removed iron parts when passing the permanent magnetic tube,then goes into the bin for pellet mill. The bin’s 2-4 hours’ capacity of the pellet mill. It has two advantages. One, if we have less workers or limited power supply,we can produce powder feed first,and then shut down previous equipments,all workers comes to the pelleting and packing system;two, by distribute pellet and powder product into different product bin,we can produce both pellet and powder feed at the same time.
The pellet mill has three layers.the top layer is the speed-adjustable feeder.It is connected with a control box. By adjusting the control box,we can change the feeding speed faster or slower to ensure the full load working of the pellet mill.
The second layer is the conditioner.It is connected with the steam supply. Powder feeds are mixed with steam in the conditioner,and are softened and cured for easier pelletizing.
The third layer is the ring die pellet machine. Feeds from the conditioner are pressed into pellet by it. By changing different ring dies we can produce pellets of different sizes.
The new made pellets’ temperature is more than 80°C,so they can not be packed directly. We use counter-flow cooler to cool them to 3-4°C more than the room temperature. Cold air goes through the intervals of the pellet and bring the heat away,then we can get cooled pellet for the next sections.
The last equipment of this section is the crumbler.It can press big pellets into small pellets by its rollers.
The fifth section: the packing section.
The task of this section is to settle the final product into the final product bin and then pack the final product in a fixed quantity.
The process is: Feed from the last section goes into the rotary screener. There’re two screen layers of different sizes in it. It can distribute big pellets back to the crumbler to be pressed again,powders back to the pell mill.and required product pellet directly into product bin to be packed.
The packing scale consists of mechanism and computer control system.The mechanism consists of feeding device,packing scale, sewing and conveyor, control system consists of weighing sensors,weighing meters and PLC programmers. It’s weighing process is like fueling the cars. First fast feed to a rated value and then slow down to the final value.By this process we can ensure the accuracy of weighing. Weighed products are put into bags,sewed and conveyed by the sewing and conveyor.
Main parameters of poultry feed machine:
Model | SZLH250 | SZLH320 | SZLH350 | SZLH400 | SZLH420 | SZLH508 |
Main Motor Power (kw|) | 22 | 37 | 55 | 90 | 110 | 160 |
Conditioner Power (kw) | 1.5 | 2.2 | 2.2 | 3 | 5.5 | 7.5 |
Dia of mould (mm) | 250 | 320 | 350 | 400 | 420 | 508 |
Feeder Power (kw) | 0.75 | 1.5 | 1.5 | 1.5 | 1.5 | 2.2 |
Size of Finished pellets (mm) | 1.5-18 | 1.5-18 | 1.5-18 | 1.5-18 | 1.5-18 | 1.5-18 |
Yeild (t/h) | 1-2 | 2-4 | 2-6 | 3-8 | 4-12 | 4-18 |
Main accessories:
1. The bearing in the pellet machine we mainly adopt the Swiss SKF.
2. The motor is Siemens.
3. The conditioner is stainless.
4. Gear wheel mainly adopts American CPM.
Spare part | Brand Name |
Electric motor | SIEMENS (Germany) |
Level detector | Autonics (Korea) |
Crusher Bearing | NSK(Japan) |
Pellet machine bearing | SKF(Sweden) |
IPC(industrial personal computer) | ADVANTECH Industrial Controlled Computer (Taiwan) |
position switches | Omron (Japan) |
Reduction box | Itc cathay Pacific (Jiangsu China) |
Main photos of 2013 high quality CE approved poultry feed machine:
Service commitment:
1. 24 hours rapid response for full-time.
2. We make maintenance plans for each equipment from our factory.
3. We provide operating training for every customer.
4. We remind the customer termly to maintain the machine.
Packing condition:
1. According to specific size of each equipment, we twine thick plastic coating for each machine.
2. Tight the equipment in the truck without space to ensure no rubbing during the transportation.
Overseas customers:
Warm welcome for your visiting our company!!!
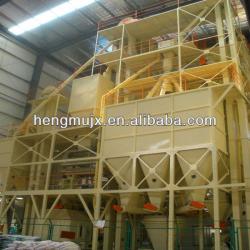
Packaging Detail:1. Wooden or metal case according to specific size of each equipment, we twine thick plastic coating for each machine. 2. Tight the equipment in the truck without space to ensure no rubbing during the transportation. |
Delivery Detail:40-45days after receiving advance |