Aluminium extrusion press
Place of Origin:Guangdong China (Mainland) | Brand Name:XQ | Model Number:1800MT(2000UST) | For getting aluminium profile:for get aluminium products |
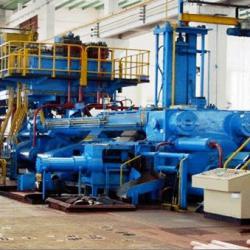
1.Aluminum extrusion press
2.Aluminum extrusion press machine
3.Aluminum extrusion press
4.Aluminum profile extrusion
Advantages of Andon Extruder
Mechanical features
·All of the main components are made of forged steel to guarantee the maximum quality and reliability of the parts
·The columns could be prestressed on the whole length, at a value of 20% greater than the value induced by the maximum extrusion force, to reduce the elongation during operation, thereby significantly increasing their resistance to fatigue.
·F.E.M analyses are regularly performed on the parts most subject to fatigue in order to guarantee the necessary useful life and to calculate the status of stress and deformation of the platen and the pressure ring, in order to minimize deformations of the die during extrusion.
·The container is thermo-regulated to guarantee improved control of processing
·The lateral displacement of the stem allows lubrication of the during introduction of the billet onto the container; Without increasing the dead cycle time.
·Mounting of the lateral and container cylinders on the sides of the press allows a quick replacement of the container and good accessibility for maintenance operations
·The longitudinal movement (tilting)of the shears guarantees a perfect cut that grazes the surface of the die and avoids scratches of the remaining material during the return phase, which could create defects in the extruded profile.
·The optional “Bolster shear” can be installed to permit cutting of the profiles between the bolster and the die for easy cleaning operations or possibly ,re-use the bolster with the next die .
Hydraulic features
All of the hydraulic components the press is equipped with are manufactured by highly qualified suppliers, such as Rexroth , Oil gear , Pall , etc. , which is a guarantee of the utmost reliability of the parts and the availability of spare parts. The following special features are foreseen.
The hydraulic circuit is realized according to the “one manifold” philosophy and is manufactured from forged steel to reduce joints in the piping to a minimum and facilitate maintenance.
The drop in pressure through the logical elements is limited in order to avoid heating oil.
Oil speed through the output and suction pipes is kept low in order to avoid heating and excessive energy loss.
The power and the capacity of the main pumps are strictly controlled in order to optimize the use of installed power, depending on the working cycle.
Electronics
Management of sequences and relevant hydraulic plant alarms (pumps, tank, etc.) with the possibility of blocking the press in the event of serious anomalies.
Cycles may be performed in manual and maintenance modes and the extrusion cycle may be managed automatically
Full control of ramp speed of the stem during the “break through” sequence, depending on the type of die mounted (soft start with complex dies, or fast start with dies that allows it).
“Slow-end function” to automatically slow down the stem when extrusion is completed, depending on the type of profile and extrusion speed, to avoid profile stretching.
Automatic control of butt end thickness.
Automatic cycles for the extrusion of 1/2, 1 ,2 or more billets with the die emptying cycle and automatic selection of the first billet for the die filling cycle.
Automatic “call ” system for billets , in accordance with the position of the cylinder ( which can be selected directly from the control panel )
Container temperature control performed with heating elements and air-cooling.
Anomalies and alarms management with automatic processing sequence stop in situations at risk.
The diagnostics of the machine provides visualization on the control panel of the reasons for eventual operational problems.
Possibility to perform an dry cycle test . The function allows performance of a complete cycle without billets , for maintenance purposes.
Revamping
ATC makes their experience and competence available. Even in revamping of existing extrusion presses. In particular. In of the company’s historical businesses, which it continues to perform, is the replacement of obsolete parts of existing presses with the company’s own components, of a more up to date conception, designed with application of the latest technologies employed in new ATC presses. And performs updating of the electrical and hydraulic units to reduce dead cycle time. The transformation of long stroke presses into short stroke presses has been particularly successful, with the replacement of the moveable crosshead and applying the system of stem displacement, which permits an increase in the maximum length of the billet and a decrease in dead cycle time, significantly increasing the productivity of the machine.
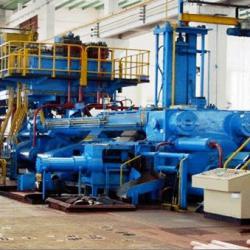
Packaging Detail:standard export packing |
Delivery Detail:3-6months |